Since 2014, the electric vehicle industry has gradually become hot. Among them, the vehicle thermal management of electric vehicles has gradually become hot. Because the range of electric vehicles depends not only on the energy density of the battery, but also on the thermal management system technology of the vehicle. The battery thermal management system has also experienced a process from scratch, from neglect to attention.
So today, let's talk about the thermal management of electric vehicles, what are they managing?
Similarities and differences between electric vehicle thermal management and traditional vehicle thermal management
This Point is put in the first place because after the automotive industry has entered the new energy era, the scope, implementation methods and components of thermal management have changed greatly.
There is no need to say more about the thermal management architecture of traditional fuel vehicles here, and professional readers have been very clear that traditional thermal management mainly includes the air-conditioning thermal management system and the thermal management subsystem of the powertrain.
The thermal management architecture of electric vehicles is based on the thermal management architecture of fuel vehicles, and adds the electric motor electronic thermal management system and battery thermal management system, unlike fuel vehicles, electric vehicles are more sensitive to temperature changes, temperature is a key factor to determine its safety, performance and life, thermal management is a necessary means to maintain the appropriate temperature range and uniformity. Therefore, the battery thermal management system is particularly critical, and the thermal management of the battery (heat dissipation/heat conduction/heat insulation) is directly related to the safety of the battery and the consistency of the power after long-term use.
So, in terms of details, there are mainly the following differences.
Different heat sources of air conditioning
The air conditioning system of traditional fuel truck is mainly composed of compressor, condenser, expansion valve, evaporator, pipeline and other components.
When cooling, the refrigerant (refrigerant) is done by the compressor, and the heat in the car is removed to reduce the temperature, which is the principle of refrigeration. Because the compressor work needs to be driven by the engine, the refrigeration process will increase the burden of the engine, and this is the reason why we say that the summer air conditioning costs more oil.
At present, almost all fuel vehicle heating is the use of heat from the engine coolant coolant - a large amount of waste heat generated by the engine can be used to warm the air conditioning. The coolant flows through the heat exchanger (also known as the water tank) in the warm air system, and the air transported by the blower is heat exchanged with the engine coolant, and the air is heated and then sent into the car.
However, in the cold environment, the engine needs to run for a long time to raise the water temperature to the right temperature, and the user needs to endure the cold for a long time in the car.
The heating of new energy vehicles mainly relies on electric heaters, electric heaters have wind heaters and water heaters. The principle of the air heater is similar to that of the hair dryer, which directly heats the circulating air through the heating sheet, thus providing hot air to the car. The advantage of the wind heater is that the heating time is fast, the energy efficiency ratio is slightly higher, and the heating temperature is high. The disadvantage is that the heating wind is particularly dry, which brings a feeling of dryness to the human body. The principle of the water heater is similar to that of the electric water heater, which heats the coolant through the heating sheet, and the high-temperature coolant flows through the warm air core and then heats the circulating air to achieve interior heating. The heating time of the water heater is slightly longer than that of the air heater, but it is also much faster than that of the fuel vehicle, and the water pipe has heat loss in the low temperature environment, and the energy efficiency is slightly lower. The Xiaopeng G3 uses the water heater mentioned above.
Whether it is wind heating or water heating, for electric vehicles, power batteries are needed to provide electricity, and most of the electricity is consumed in air conditioning heating in low temperature environments. This results in reduced driving range of electric vehicles in low temperature environments.
Compared with the problem of slow heating speed of fuel vehicles in low temperature environments, the use of electric heating for electric vehicles can greatly shorten the heating time.
Thermal management of power batteries
Compared with the engine thermal management of fuel vehicles, the thermal management requirements of electric vehicle power system are more stringent.
Because the best working temperature range of the battery is very small, the battery temperature is generally required to be between 15 and 40 ° C. However, the ambient temperature commonly used by vehicles is -30~40 ° C, and the driving conditions of actual users are complex. Thermal management control needs to effectively identify and determine the driving conditions of vehicles and the state of batteries, and carry out the optimal temperature control, and strive to achieve a balance between energy consumption, vehicle performance, battery performance and comfort.
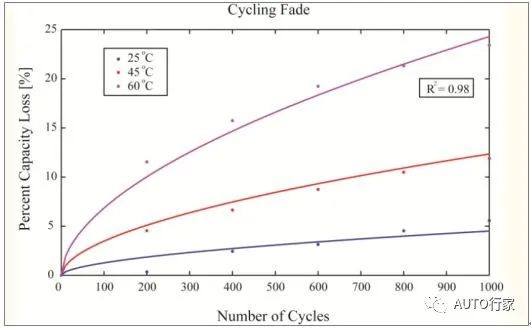
In order to alleviate range anxiety, electric vehicle battery capacity is getting larger and larger, and energy density is getting higher and higher; At the same time, it is necessary to solve the contradiction of too long charging waiting time for users, and fast charging and super fast charging came into being.
In terms of thermal management, high current fast charging brings greater heat generation and higher energy consumption of the battery. Once the battery temperature is too high during charging, it may not only cause safety risks, but also lead to problems such as reduced battery efficiency and accelerated battery life decay. The design of thermal management system is a severe test.
Electric vehicle thermal management
Occupant cabin comfort adjustment
The indoor thermal environment of vehicle directly affects the occupant's comfort. Combining with the sensory model of human body, the study of flow and heat transfer in the cab is an important means to improve the vehicle comfort and improve the vehicle performance. From the body structure design, from the air conditioning outlet, the vehicle glass affected by sunlight radiation and the whole body design, combined with the air conditioning system, the impact on occupant comfort is considered.
When driving a vehicle, users should not only experience the driving feeling brought by the strong power output of the vehicle, but also the comfort of the cabin environment is an important part.
Power battery operating temperature adjustment control
Battery in the use of the process will encounter a lot of problems, especially in the battery temperature, lithium battery in the extremely low temperature environment power attenuation is serious, in the high temperature environment is prone to safety risks, the use of batteries in extreme cases will be very likely to cause harm to the battery, thereby reducing battery performance and life.
The main purpose of thermal management is to make the battery pack always work within the appropriate temperature range to maintain the best working condition of the battery pack. The thermal management system of the battery mainly includes three functions: heat dissipation, preheating and temperature equalization. Heat dissipation and preheating are mainly adjusted for the possible impact of the external environment temperature on the battery. Temperature equalization is used to reduce the temperature difference within the battery pack and prevent the rapid decay caused by overheating of a certain part of the battery.
The battery thermal management systems used in the electric vehicles now on the market are mainly divided into two categories: air-cooled and liquid-cooled.
The principle of the air-cooled thermal management system is more like the heat dissipation principle of the computer, a cooling fan is installed in one section of the battery pack, and the other end has a vent, which accelerates the flow of air between the batteries through the work of the fan, so as to take away the heat emitted by the battery when it is working.
To put it bluntly, air cooling is to add a fan on the side of the battery pack, and cool the battery pack by blowing the fan, but the wind blown by the fan will be affected by external factors, and the efficiency of air cooling will be reduced when the outside temperature is higher. Just like blowing a fan doesn't make you cooler on a hot day. The advantage of air cooling is simple structure and low cost.
Liquid cooling takes away the heat generated by the battery during work through the coolant in the coolant pipeline inside the battery pack to achieve the effect of reducing the battery temperature. From the actual use effect, the liquid medium has a high heat transfer coefficient, large heat capacity, and faster cooling speed, and Xiaopeng G3 uses a liquid cooling system with higher cooling efficiency.

In simple terms, the principle of liquid cooling is to arrange a water pipe in the battery pack. When the temperature of the battery pack is too high, cold water is poured into the water pipe, and the heat is taken away by cold water to cool down. If the battery pack temperature is too low, it needs to be heated up.
When the vehicle is driven vigorously or charged quickly, a large amount of heat is generated during the charging and discharging of the battery. When the battery temperature is too high, turn on the compressor, and the low-temperature refrigerant flows through the coolant in the cooling pipe of the battery heat exchanger. The low-temperature coolant flows into the battery pack to take away the heat, so that the battery can maintain the best temperature range, which greatly improves the safety and reliability of the battery during the use of the car and shortens the charging time.
In the extremely cold winter, due to low temperature, the activity of lithium batteries is reduced, the battery performance is greatly reduced, and the battery cannot be high-power discharge or fast charging. At this time, turn on the water heater to heat the coolant in the battery circuit, and the high temperature coolant heats up the battery. It ensures that the vehicle can also have fast charging ability and long driving range in low temperature environment.
Electric drive electronic control and high power electrical parts cooling heat dissipation
New energy vehicles have achieved comprehensive electrification functions, and the fuel power system has been changed to an electric power system. The power battery outputs up to 370V DC voltage to provide power, cooling and heating for the vehicle, and supply power to various electrical components on the car. During the driving of the vehicle, high-power electrical components (such as motors, DCDC, motor controllers, etc.) will generate a lot of heat. The high temperature of power appliances may cause vehicle failure, power limitation and even safety hazards. Vehicle thermal management needs to dissipate the generated heat in time to ensure that the high-power electrical components of the vehicle are in the safe working temperature range.
G3 electric drive electronic control system adopts liquid cooling heat dissipation for thermal management. The coolant in the electronic pump drive system pipeline flows through the motor and other heating devices to carry away the heat of the electrical parts, and then flows through the radiator at the front intake grille of the vehicle, and the electronic fan is turned on to cool the high-temperature coolant.
Some thoughts on the future development of thermal management industry
Low energy consumption:
In order to reduce the large power consumption caused by air conditioning, heat pump air conditioning has gradually received high attention. Although the general heat pump system (using R134a as the refrigerant) has certain limitations in the environment used, such as extremely low temperature (below -10 ° C) can not work, refrigeration in high temperature environment is no different from ordinary electric vehicle air conditioning. However, in most parts of China, the spring and autumn season (ambient temperature) can effectively reduce the energy consumption of air conditioning, and the energy efficiency ratio is 2 to 3 times that of electric heaters.
Low noise:
After the electric vehicle does not have the noise source of the engine, the noise generated by the operation of the compressor and the front-end electronic fan when the air conditioner is turned on for refrigeration is easy to be complained by users. Efficient and quiet electronic fan products and large displacement compressors help reduce the noise caused by operation while increasing the cooling capacity
Low cost:
The cooling and heating methods of thermal management system mostly use liquid cooling system, and the heat demand of battery heating and air conditioning heating in low temperature environment is very large. The current solution is to increase the electric heater to increase the heat production, which brings high parts cost and high energy consumption. If there is a breakthrough in battery technology to solve or reduce the harsh temperature requirements of batteries, it will bring great optimization in the design and cost of thermal management systems. The efficient use of the waste heat generated by the motor during the running of the vehicle will also help reduce the energy consumption of the thermal management system. Translated back is the reduction of battery capacity, the improvement of driving range, and the reduction of vehicle cost.
Intelligent:
A high degree of electrification is the development trend of electric vehicles, and traditional air conditioners are only limited to refrigeration and heating functions to develop intelligentized. Air conditioning can be further improved to big data support based on user car habits, such as family car, the temperature of the air conditioning can be intelligently adapted to different people after they get on the car. Turn on the air conditioning before going out so that the temperature in the car reaches a comfortable temperature. The intelligent electric air outlet can automatically adjust the direction of the air outlet according to the number of people in the car, the position and the size of the body.
Post time: Oct-20-2023